CSR is the name behind some of Australia and New Zealand’s most trusted and recognised building products for construction of homes and commercial buildings
Our Brands
Our Brands
Corporate Headquarters
Triniti 3, 39 Delhi Road, North Ryde, NSW 2113, Australia
Telephone : +61 2 9235 8000
CSR Limited 2024, All rights reserved Privacy Policy Website Terms of Use
This website uses cookies. For further details, please review our Website Terms and Conditions
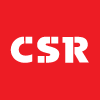
Corporate Headquarters
Triniti 3, 39 Delhi Road, North Ryde, NSW 2113, Australia
Telephone : +61 2 9235 8000
CSR Limited 2024, All rights reserved
